Hidden Facts the Ready Mix Concrete Industry Keeps Quiet!
Category :
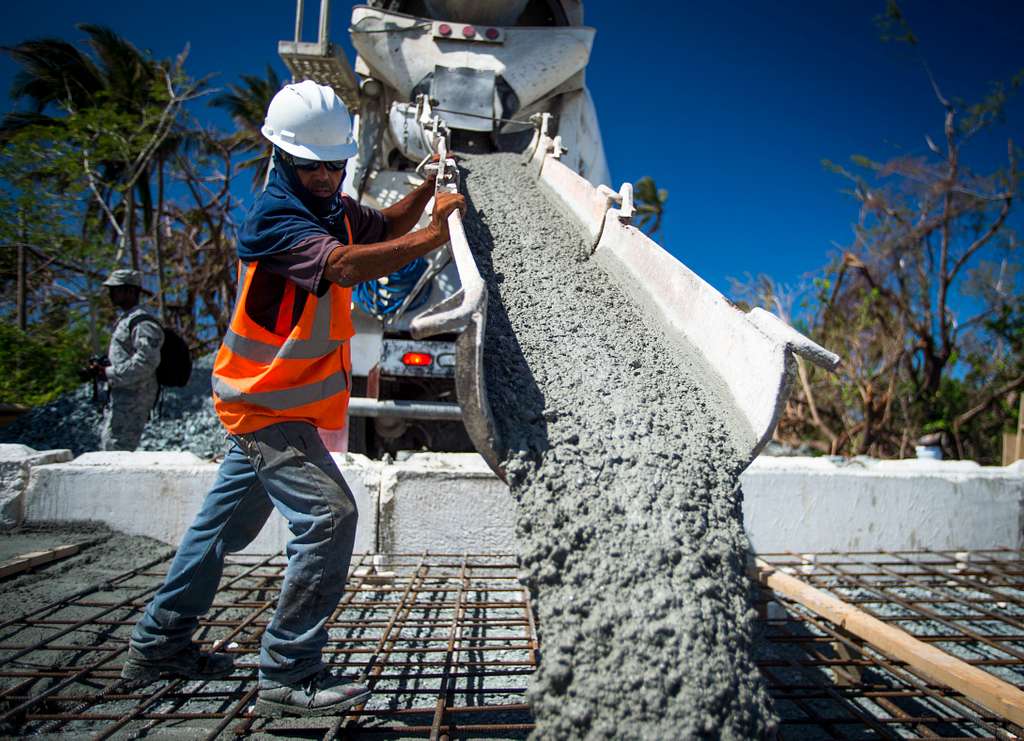
Ready mix concrete, an essential component in modern construction, revolutionizes how projects are managed and executed. However, beneath the surface of this innovative material are lesser-known facts that the industry often does not spotlight. This blog post delves into these hidden details, providing a deeper understanding of ready mix concrete and revealing what you need to know before choosing it for your next project.
Understanding Ready Mix Concrete
Ready mix concrete serves as the backbone of countless construction projects, providing a tailored solution that's both time-efficient and versatile. But what exactly goes into this seemingly straightforward material, and what should you know to make the most of its benefits?
The Basics of Ready Mix Concrete
Ready mix concrete is not just any concrete; it is meticulously prepared and mixed at a batching plant according to specific job requirements. This customization ensures that the mix is perfectly suited to its intended application, whether it’s a residential driveway or a large-scale commercial foundation.
Components of Ready Mix Concrete
The fundamental ingredients of ready mix concrete remain consistent: Portland cement, aggregates (like sand and gravel), and water. However, the magic lies in the proportions and any additional admixtures. These can include:
- Air-entraining agents to improve freeze-thaw resistance.
- Retarders to delay the setting time, especially useful in hot climates.
- Superplasticizers to enhance flowability without increasing water content.
Each ingredient is selected based on its quality, source, and compatibility with the mix, ensuring the final product is not only durable but also consistent from batch to batch.
Production and Quality Control
The production of ready mix concrete is a precise operation involving stringent quality control measures. From the initial selection of materials to the final mixing, everything is monitored closely. This rigorous process includes:
- Batching: Ingredients are measured with high precision to ensure the mix ratio is exactly right.
- Mixing: Components are blended in industrial mixers to achieve a homogeneous mixture.
- Transportation: The mixed concrete is transported to the site using concrete mixer trucks that keep the concrete in motion to prevent it from setting prematurely.
Why Opt for Ready Mix Concrete?
Choosing ready mix concrete offers several advantages, notably:
- Quality Assurance: With controlled production conditions, ready mix concrete offers superior uniformity and quality compared to on-site mixed concrete.
- Versatility: Modifications to the mix design allow for a wide range of properties to meet different construction needs.
- Convenience and Speed: Delivered ready to use, it reduces on-site labor and significantly cuts down construction time.
- Reduced Waste: Precise mixing reduces material wastage, which is both cost-effective and environmentally friendly.
- Sustainability Options: Modern ready mix plants often use recycled materials and renewable energy sources, enhancing the green credentials of your project.
What the Industry Often Doesn't Tell You
While ready mix concrete is a staple in the construction industry, known for its reliability and efficiency, there are several aspects that are not typically discussed openly with consumers. These lesser-known facts can significantly impact project outcomes, cost efficiency, and overall satisfaction.
Variability in Material Sources
The quality of ready mix concrete hinges largely on the origin and quality of the raw materials used. Suppliers might source their cement, aggregates, and additives from various providers, leading to subtle differences in the final product's quality. While industry standards are in place to ensure consistency, slight variations are inevitable and can affect the strength and durability of the concrete.
Precision in Mixing
The precise mixing of concrete ingredients is critical to achieving the desired strength and workability. However, even with advanced technology, human error and equipment inconsistencies can introduce variability. This factor is seldom disclosed upfront but can influence the performance of the concrete once it is laid.
Cost Dynamics and Long-Term Considerations
Initial Cost vs. Lifetime Value
The upfront cost of ready mix concrete might appear attractive, but that's not the whole story. Depending on the mix and the environmental conditions at the project site, maintenance and repair costs over the concrete's lifespan could offset any initial savings. Industry insiders know this well but might not make it a point of discussion during the procurement process.
Environmental Adjustments
Concrete mixes are often adjusted to perform under specific environmental conditions, such as extreme temperatures or exposure to seawater. These adjustments can add to the cost, and if not done correctly, can compromise the longevity and effectiveness of the concrete. This critical detail requires transparency to ensure the right mix is used for the right conditions.
Sustainability Issues
The production of ready mix concrete contributes significantly to carbon emissions and energy consumption. Though strides are being made towards greener alternatives, such as using recycled materials and reducing the clinker content in cement, these practices are not universally adopted. The industry is often quiet about the environmental footprint of concrete production, which is an essential consideration for environmentally conscious clients.
Water Usage
The amount of water used in producing concrete is considerable. Inefficient water use can lead to higher operational costs and environmental strain. Innovations in water recycling and reduced water mixes are available, yet they are not standard practice, and their benefits and availability are not always communicated effectively.
Key Metrics in Ready Mix Concrete Delivery
Delivering ready mix concrete efficiently and effectively requires understanding several crucial metrics. These figures are not just numbers; they are pivotal factors that influence the success and timing of construction projects. Here’s a detailed breakdown of the key metrics thatdefine ready mix concrete delivery.
Standard Truck Capacity
The typical capacity of a ready mix concrete truck ranges from 8 to 12 cubic yards. However, the most common size seen on most projects can carry approximately 10 cubic yards of concrete. This capacity is carefully chosen to balance the weight limits set by local transport authorities with the need to minimize the number of deliveries.
Determining the Number of Deliveries
Knowing the capacity of a concrete truck helps in planning how many deliveries are required for a project. For instance, if a project needs 50 cubic yards of concrete, it would ideally require five truckloads. Accurate calculation here helps avoid delays or excess concrete that might result from miscalculations.
How Many Yards in a Truckload?
The term "yards" refers to cubic yards, which is the standard measure of volume used for concrete. As mentioned, a typical truckload is about 10 cubic yards. This metric is crucial for project managers to understand as it directly affects project planning and the scheduling of pours.
What Does 'Concrete Go' Mean?
The phrase "concrete go" refers to the readiness state of concrete for pouring immediately upon arrival at the job site. It signifies that the concrete has maintained its optimal mix consistency during transit and is ready to be used without any need for additional mixing or adjustments.
Timing and Coordination
Delivering ready mix concrete isn't just about transporting a product; it’s about precise timing and coordination. The concrete needs to reach the site before it starts to cure but also at a time when the site is prepared for pouring. Delays can compromise the integrity of the concrete, leading to weakened structures or the need for additional product.
Maintaining Mix Consistency
Ensuring the concrete maintains its specified mix consistency during transit is vital. Concrete trucks are equipped with rotating drums that keep the concrete in motion to prevent it from setting. The speed and duration of this rotation are carefully controlled based on the travel time and environmental conditions.
Fresh Insights and Lesser-Known Tips
- Temperature Sensitivity: Concrete's curing time and strength can vary significantly with temperature changes. Industry professionals manage this with additives that are rarely discussed with clients.
- Environmental Impact: While concrete is durable, its production is energy-intensive and emits considerable CO2. However, newer, greener alternatives are being developed that the industry is only beginning to adopt broadly.
Practical Advice for Consumers
When considering ready mix concrete for a project, it’s important to:
- Assess Supplier Credibility: Check the reputation and track record of the concrete supplier.
- Understand Your Needs: Calculate the exact amount of concrete your project requires to avoid underestimating or overpaying.
- Consider the Project Environment: Ensure the concrete mix is suitable for the environmental conditions of the project site.
Conclusion
The ready mix concrete industry, like any other, has its secrets and subtleties. By arming yourself with the knowledge provided here, you can navigate your construction projects more effectively and avoid common pitfalls. Always strive for transparency with your suppliers and insist on the highest quality materials for your construction needs.