How to Choose the Right Cable Chain for Your Machine
Category :
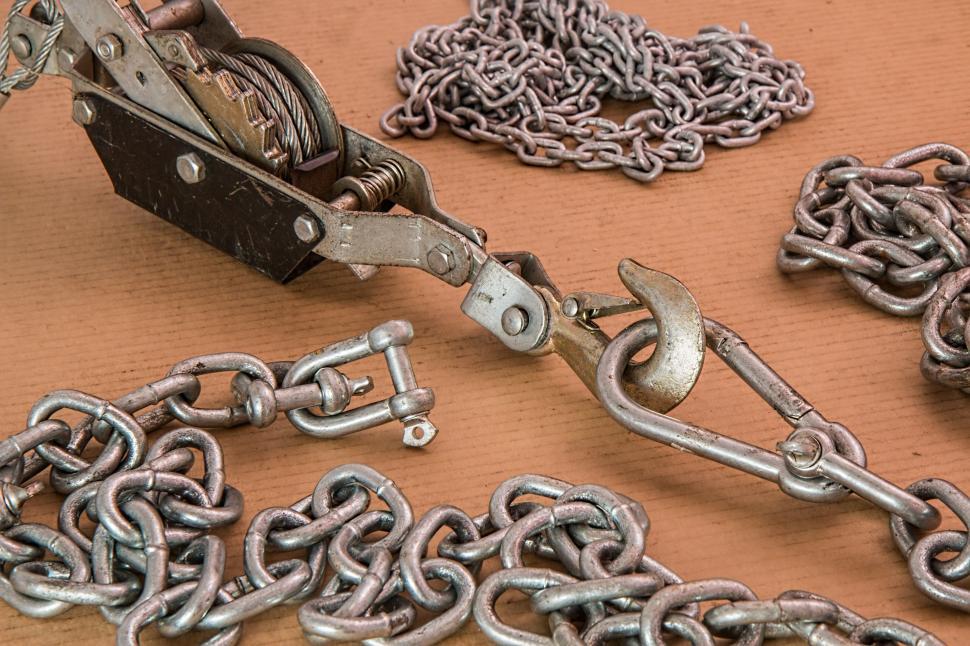
Selecting the right cable chain for your machine is crucial to enhancing its efficiency and prolonging its lifespan. Cable chains, also known as drag chains or energy chains, are essential components used to protect and manage cables in dynamic applications. This article will guide you through the process of choosing the appropriate cable-chain, considering various types of machines and their specific requirements.
Introduction to Cable Chains
Cable chains are designed to enclose and guide flexible cables and hoses connected to moving automated machinery. They minimize wear and tear on cables, prevent entanglement, and enhance operational safety. Understanding the different types of cable-chains and their applications can significantly impact machine performance.
Understanding Your Machine's Requirements
Before diving into the selection process, it's essential to understand your machine's specific needs:
Type of Movement: Determine if your machine requires a cable-chain for linear, rotary, or three-dimensional movements.
Environment: Consider the environmental factors such as exposure to chemicals, temperature, and mechanical abrasions.
Size and Weight of Cables: Assess the number and type of cables or hoses that the chain needs to accommodate.
Detailed Overview of Cable Chain Types
When choosing the right cable-chain for your machine, understanding the different types available is crucial. Each type is suited to specific applications based on environmental conditions, load requirements, and movement types. Here's a closer look at the main types of cable-chains:
- Standard Cable Chains:
Description: These are the most commonly used cable-chains across various industries. Made primarily from high-strength plastic, they are lightweight yet durable enough to handle light to medium loads.
Applications: Ideal for general automation machinery, printing equipment, and light robotic arms where the chain experiences less stress and environmental aggression.
- Heavy-Duty Cable Chains:
Description: Constructed from reinforced materials such as steel or robust plastics, these chains are designed to withstand heavy loads and high stress. They often feature a more rugged design to cope with the demanding conditions.
Applications: Best suited for construction equipment, heavy manufacturing machinery, and applications involving extreme temperatures or abrasive conditions where additional strength and durability are necessary.
- Enclosed Cable-Chains:
Description: These cable-chains are designed with a closed design to protect cables from dust, debris, and other particulates. This makes them perfect for environments where contamination could lead to significant downtime or damage.
Applications: Commonly used in woodworking, milling, and other dusty environments. Also ideal for outdoor applications where exposure to the elements is a concern, such as in marine or heavy weather conditions.
- Robot-Specific Cable-Chains:
Description: Tailored for robotic applications, these chains are extremely flexible and can support the complex movements of robotic arms. They are designed to prevent twisting and tangling of cables during multi-axis movements.
Applications: Robotics, especially in automotive assembly lines or precision tasks where robots move in multiple directions and require consistent cable management to avoid operational failures.
Key Factors to Consider When Choosing a Cable Chain
When it comes to selecting the appropriate cable-chain for your machinery, understanding several key factors can greatly influence the decision-making process. These considerations ensure that the chosen cable-chain will perform optimally under the specific conditions of your machine’s operation. Here's a more in-depth look at what to consider:
Material: The material of the cable-chain is crucial because it must withstand the operational environment without degrading.
Plastic: Ideal for environments free from extreme temperatures and harsh chemicals, plastic chains are lightweight and suitable for high-speed operations.
Steel: For machines operating under rugged conditions, such as exposure to high temperatures and corrosive substances, steel chains are preferable for their superior durability and strength.
Hybrid (Plastic and Metal): These chains offer a middle ground, providing the lightweight nature of plastic and the durability of steel, making them suitable for a variety of applications.
Size and Flexibility: It’s vital to choose a cable-chain that fits the physical dimensions and flexibility needs of your cables.
Chain Dimensions: Ensure the cable-chain has enough space to accommodate all cables and hoses comfortably without squeezing them. Too tight a fit can cause friction and wear, while too loose a fit might lead to tangling or snagging.
Bending Radius: The minimum bending radius of the cable-chain should match or exceed the flexibility requirements of the cables it houses. This is essential to prevent the cables from kinking or breaking, which can lead to system failures.
Load Capacity:
Weight Tolerance: Verify the chain’s capacity to handle the weight of the cables and hoses it will contain. Underestimating load capacity can lead to the chain breaking or deforming.
Dynamic vs. Static Loads: Consider whether the load will primarily be static or if the chain will need to accommodate significant movement. Dynamic loads require a more robust design to handle the constant motion without deteriorating.
Speed and Acceleration:
Operational Speeds: Some cable chain are specifically designed to cope with higher speeds by reducing noise and resisting the forces that may cause the chain to stretch or wear prematurely.
Acceleration: If your machinery involves rapid starts and stops, the cable-chain needs to withstand these forces without letting the cables inside slip or jerk, which could damage them.
Environmental Considerations:
Exposure to Chemicals: If your machine operates in an environment with chemical exposure, the cable chain material must resist corrosion or degradation.
Temperature Range: The chain should maintain its integrity and functionality over the full range of temperatures it will be exposed to.
Dust and Debris: In dusty or particle-rich environments, consider an enclosed cable chain to protect the cables from being clogged with debris, which could impair their function.
Choosing Based on Specific Applications
Cobra Cable Chain Size Chart: Use this chart for selecting chains that fit the specific dimensions and bending radii of your cables.
Liquid Wrench Chain and Cable Lube: This product is essential for maintaining the chain’s flexibility and reducing wear.
Cable Chain for Snow Machines: When choosing cable-chains vs. tire chains, consider the specific requirements for traction and durability in snowy conditions.
Installation and Maintenance of Cable Chains
Proper installation and diligent maintenance of cable chains are essential to ensuring the reliability and longevity of your machine’s cable management system. Here’s a detailed guide on how to effectively install and maintain cable chains for optimal performance.
Preparation:
Assess Requirements: Before installation, make sure you have the correct size and type of cable-chain for your application. Verify that the chain’s dimensions are suitable for the cables and hoses it needs to house.
Gather Tools and Materials: Depending on the type of cable chain, you may need various tools for installation. Commonly required items include screwdrivers, pliers, and mounting brackets.
Mounting the Chain:
Fixing Points: Identify and prepare the points where the chain will attach to the machine. These should allow for full range of motion without straining the cables.
Secure the Ends: Attach the ends of the cable chain to the machine using the brackets provided or recommended by the manufacturer. Ensure that all connections are tight and secure to prevent any movement that could lead to wear or disconnection.
Loading the Cables:
Insert Cables: Carefully place the cables and hoses inside the compartments of the cable chain. Avoid twisting or forcing the cables, as this can damage them.
Maintain Spacing: Ensure there is sufficient space between each cable to prevent friction and overheating. Use separators if provided to keep cables organized and in place.
Testing the Chain:
Manual Movement: Once the cables are in place, manually move the chain through its full range of motion to check for any binding or snagging.
Operational Test: Run the machine at low speeds initially to monitor the cable-chain’s performance. Look for smooth operation and listen for any unusual noises which might indicate a problem.
Maintenance Guidelines
Regular Inspections:
Visual Checks: Regularly inspect the cable chain for signs of wear such as cracks, deformations, or loose components. Early detection of issues can prevent more serious problems and machine downtime.
Functional Testing: Periodically test the movement of the cable chain during operation. Pay attention to ease of movement and any changes in noise, which could indicate wear.
Cleaning and Lubrication:
Cleaning: Keep the cable chain clean from dust, debris, and any chemical residues that might accumulate, particularly in enclosed or high-particulate environments. Cleaning helps maintain the functionality and longevity of the chain.
Lubrication: Apply suitable lubricants to the chain joints and bearings, if applicable. This reduces friction, prevents rust, and extends the life of the chain. Always use lubricants that are compatible with the materials of both the chain and the cables.
Adjustments and Replacements:
Tightening and Adjustments: Check and tighten any loose mounting brackets and joints. Adjust the tension and alignment if you notice any slippage or misalignment during operation.
Part Replacement: Replace any worn or damaged parts immediately to maintain the integrity and safety of the cable management system.
Drawback of using cable chains in machinery
Restricted Flexibility and Range of Motion: Cable-chains are designed to guide and protect moving cables, but they inherently come with limitations on the range of motion they can accommodate. Each cable-chain has a specific bending radius, which must not be exceeded to avoid damaging the cables inside. If a machine requires movements that exceed this radius, the cable chain can restrict the movement, potentially compromising the machine's functionality. This limitation can be particularly problematic in highly dynamic systems where extensive or complex movements are necessary. As such, choosing a cable-chain with an inappropriate bending radius can lead to reduced operational efficiency and increased wear on both the cables and the chain itself.
Addressing Common Questions
- What is a cable chain necklace?: While primarily an industrial component, the term "cable chain" can also refer to a type of jewelry. In industrial contexts, it's crucial not to confuse them.
- 2mm Sterling Silver Chain and 5mm Silver Chain: In contexts where precision and aesthetics are vital, even slight differences in chain size (like between 2mm and 5mm) can be significant.
- Cable Chain Bracelet: A lightweight version often used in decorative applications.
Conclusion
Choosing the right cable chain is vital for ensuring the safety and efficiency of your machinery. By considering the factors outlined, you can select a cable chain that meets your needs and enhances machine performance. Remember to regularly check and maintain your cable-chains to prevent any potential issues and ensure smooth operation.